Inventory Management Software Frequently Asked Questions: Capabilities and Industries
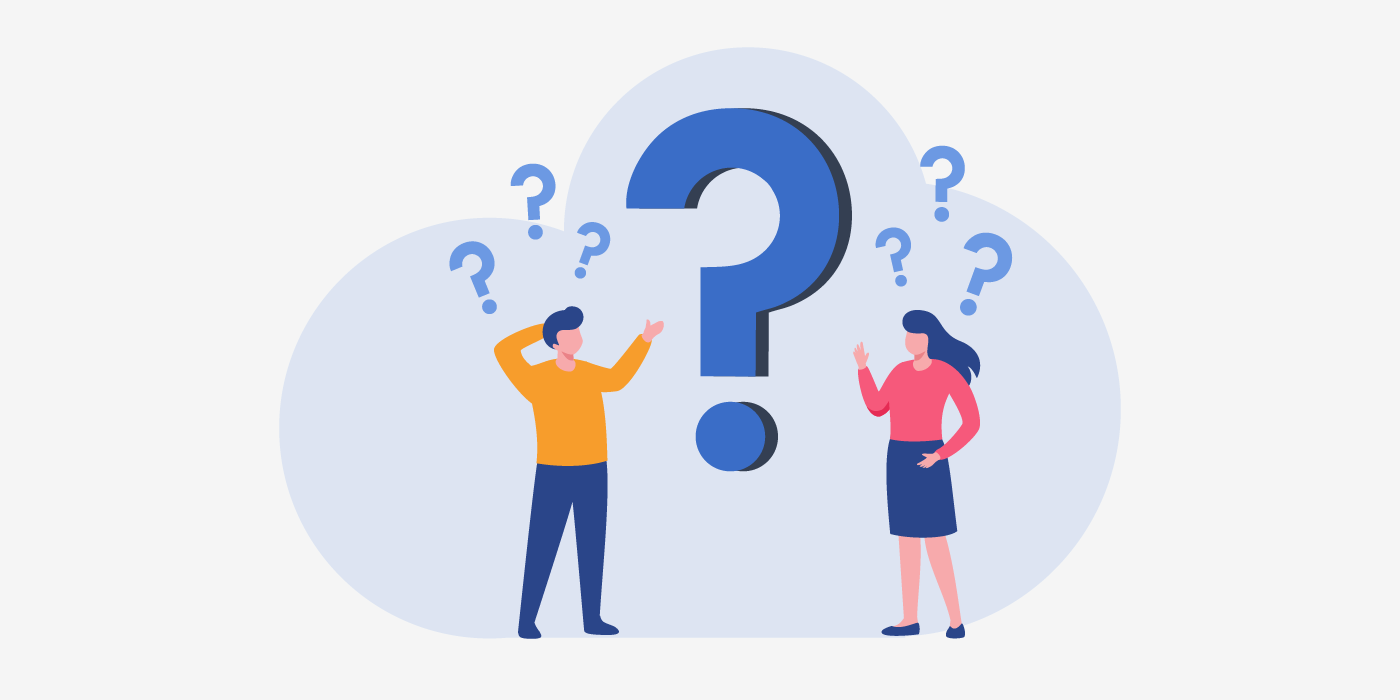
General Capabilities of eTurns TrackStock
Inventory management software can make the chore of replenishment more efficient, accurate and automated. The suite of features in eTurns TrackStock make it one of the most robust yet easy-to-use inventory replenishment apps in the industry. From simplified inventory audits with QR code scans that trigger auto-replenishment orders to in-depth AI analytics and reporting, TrackStock takes the guesswork and the heavy lifting out of inventory replenishment. Learn more below about what features are important in inventory management software.
How Does Inventory Management Software Transform Inventory Control?
Managing inventory levels to prevent stockouts without leaving excess cash in inventory is next to impossible with manual counting methods and ordering protocols that require multiple error-prone steps. Inventory management software like TrackStock makes cycle counts (inventory audits) faster and easier, replenishment ordering more automated, and analytics more accurate.
What Are the Key Features of Modern Inventory Management Systems?
The best modern inventory management systems include the following features:
-
QR code scanning apps for quick inventory counts
-
Interactive dashboards that show you inventory status
-
Automated reordering options using min/max
-
AI features that show you how much money you could save if you used optimal min/max settings
-
Weight sensors and eLabels in addition to scanning technology
-
Seamless integration capabilities
-
Reporting and analytics
Industry-Specific Inventory Management Software FAQs
Learn more about the specific features that make TrackStock an ideal fit in the following key industries.
Contracting
Contractors have to carefully track various metrics in order to ensure customer satisfaction and efficiency across multiple projects and sites. They must also balance supply needs with carrying costs and ensure that they have the necessary materials on hand to stick to agreed project timelines and avoid unplanned downtime.
How Can Inventory Management Software Benefit Contracting Companies?
Stockroom inventory management software benefits contracting companies by optimizing the tracking and management of materials, tools, and equipment across various projects and sites. Specifically, inventory management apps like TrackStock can facilitate faster inventory audits or cycle counts with QR code scans. TrackStock works in a vendor-managed inventory (VMI) or customer-managed inventory (CMI) model.
These apps can also help in more sophisticated ways like managing consigned inventory by tracking usage. This functionality can help contractors increase profitability by allowing them the ability to track usage and negotiate the return to the distributor of unused inventory at the end of a project. This case study from M & L Electrical describes how they were able to return unused inventory to Graybar and decrease the time spent counting inventory for the next day’s jobs from 2 hours/day to 5 minutes every 2 weeks using TrackStock.
Automated replenishment software like TrackStock can significantly reduce instances of over-ordering or stockouts, which are common issues in the contracting sector. By ensuring that the right materials are available at the right time, contractors can avoid project delays and minimize downtime. The software helps in accurate cost tracking and forecasting, which improves budgeting and enhances overall operational efficiency and profitability.
What Features Should Contractors Look for in Inventory Management Software?
Contractors should prioritize several key features when selecting inventory management software, including the following:
-
Barcode scans for counts and pulls from inventory
-
Ability to track consignment inventory
-
Auto-replenish using min/max settings
-
AI to optimize inventory levels
-
Reports with actionable data
-
Fewest steps possible to send an order through the app
-
Ability to track kits and lot numbers
These features combine to create a powerful tool that can handle the complexities of inventory management in the contracting industry.
Distribution
Distributors need to replenish many customers, all of whom require different inventory items and quantities. Trying to track customer stockroom inventory usage and replenishment needs by hand can lead to unhappy customers and ongoing errors.
How can a modern VMI app help a distributor be more efficient while delivering higher service levels?
A modern VMI app can significantly enhance the efficiency of distributors who have been doing VMI replenishment manually. Apps that use barcode scanning, eLabels, or sensors make counts faster, automate inventory replenishment orders, and improve accuracy in stock levels. By using VMI apps instead of manual counting, distributor reps can cover more customer accounts in a day, seamlessly send digital orders to the backend ERP system, and reduce the chance of over-stocking or understocking customer stockrooms. Improved inventory accuracy and efficiency ultimately enhance service levels, as customers receive their orders on time and with fewer errors, boosting satisfaction and loyalty.
Can Inventory Management Software Seamlessly Integrate with Existing Distribution Systems?
Modern inventory management software is designed to seamlessly integrate with a distributor’s existing business systems, such as ERP (Enterprise Resource Planning), SCM (Supply Chain Management), and WMS (warehouse management systems). This integration capability is crucial for distributors as it allows for a unified view of customer inventory replenishment, enhancing data accuracy and streamlining processes.
Vendor Managed Inventory (VMI) and Customer Managed Inventory (CMI)
Some organizations choose a VMI model for replenishment, which involves depending on suppliers to control replenishment. On the other hand, others use a CMI model so they can do self-service replenishment ordering themselves. Inventory management software can help optimize either approach.
How Is Inventory Management Software Utilized in VMI and CMI Use Cases?
Inventory management software plays a pivotal role in both VMI and CMI replenishment models at customer sites. In VMI, the software allows vendors to use QR code scans, eLabels or weight sensors to replenish customer inventory using min/max settings. VMI apps enable increased visibility from remote locations of customer stockroom/onsite inventory levels. VMI software helps vendors manage stock levels and schedule deliveries more effectively, ensuring that customers do not face stockouts or overstock situations.
In a customer-managed inventory or CMI model, inventory management software helps businesses use CMI apps in a self-service way to maintain control over replenishment orders, timing, and billing. Good CMI apps have features like TrackStock’s AI Min/Max Tuning which allow businesses to track their usage and fine tune their min/max levels in order to optimize inventory levels and save costs.
What Features Are Essential in Inventory Management Software for Supporting VMI/CMI Replenishment Processes?
Key features for VMI and CMI strategies include:
-
Automated Replenishment Using Min/Max Settings
-
Real-time Visibility
Medical, Dental and Veterinary Clinics
In medical, dental, and veterinary clinics, having the right supplies on hand is essential for the safety and satisfaction of all patients. Optimizing inventory levels can have a drastic impact on the financial wellness of the clinic.
What Ways Can Inventory Management Software Support Medical Clinic Inventory Needs?
Good inventory management software supports clinics by ensuring accurate tracking, efficient management, and automated replenishment of medical supplies and pharmaceuticals. It optimizes stock levels, reduces waste through expiration and lot number tracking, and automates reorder processes to prevent critical shortages, enhancing overall patient care. By adding visibility and automation, inventory management software allows medical professionals to spend less time on inventory counting and more time on patient care. Advanced inventory sensor technologies like electronic shelf labels are ideal for triggering the replenishment of medical supplies in space-constrained clinics.
How Can Inventory Management Software Ensure Compliance and Efficiency in Medical Inventories?
By maintaining detailed logs of inventory movements, expiration dates, and lot tracking, inventory management software can help clinics maintain compliance. This software also supports efficient operations by integrating with other records, facilitating seamless information flow and improving accuracy in inventory management. TrackStock is integrated with McKesson and Amazon Business for seamless integrated ordering.
Maintenance, Repair, and Operations (MRO)
Accurate replenishment of MRO supplies is crucial in manufacturing and industrial settings, where equipment and supplies are pivotal to the operational process. Inventory management of MRO items like spare parts, tools, janitorial/sanitation, and other supplies ensures that necessary items are available without costly overstocking.
How Can Inventory Management Software Optimize MRO Inventory Management and Cycle Counting?
Inventory management software streamlines MRO by automating cycle counting and inventory audits using QR code scanning apps like TrackStock that reduce errors and trigger automated replenishment. MRO replenishment apps like TrackStock ensure that maintenance teams always have the necessary parts available for maintenance and repairs, without carrying excess inventory.
Can Inventory Management Software Help Me Keep the Right Parts in Stock For Asset Maintenance And Send Notifications When Maintenance Is Due?
Inventory management software can effectively track inventory levels of critical parts and automatically alert teams when stock is low or when scheduled maintenance is approaching. This feature helps prevent downtime by ensuring parts are available for timely repairs and maintenance.
Service Trucks
Efficient management of service trucks requires careful tracking of parts, labor, and supplies.
How Is Inventory Management Software Utilized for Service Truck Inventory Management?
Inventory management software for service trucks helps manage and track tools, as well as resupply parts and equipment on the vehicle. This ensures that all necessary items are stocked and accounted for, enhancing efficiency in field service operations by reducing time spent on unplanned trips to resupply parts while ensuring that staff have the needed parts for every project. Inventory management software like TrackStock includes work order management for creating customer invoices with parts, labor, photos and signature capture after a service call. TrackStock work orders trigger pulls from inventory that trigger automated replenishment orders from the nearby warehouse or from suppliers.
What Features Are Important for Service Truck Inventory Management Software?
Key features include:
-
Mobile accessibility for real-time inventory tracking from anywhere
-
Barcode scanning to quickly pull items from inventory
-
Work order management that includes parts, labor, before and after photos and signature capture. The work orders should trigger pulls from inventory that trigger automated replenishment orders from the nearby warehouse or from suppliers.
These features ensure that inventory levels are accurate and that service trucks are always equipped for the job at hand, boosting job completion rates for service providers.