How to Do Point of Use Inventory Management Efficiently
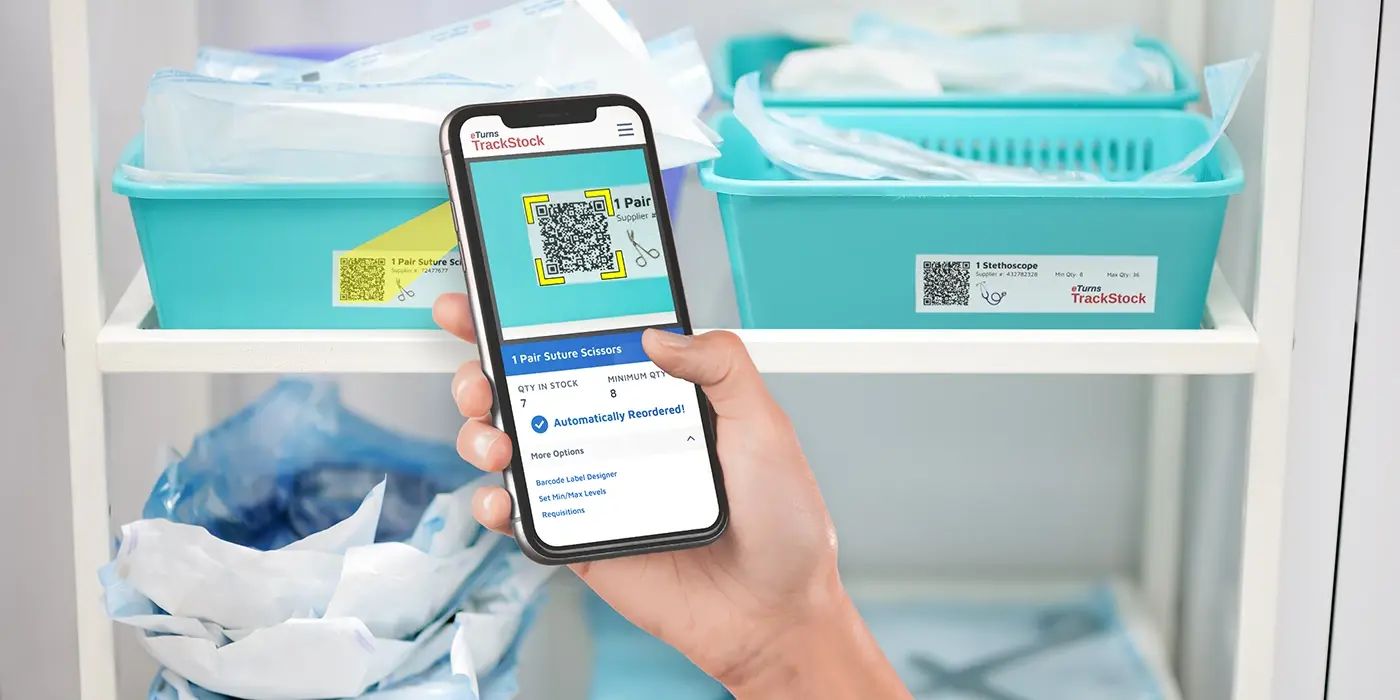
What is Point of Use Inventory?
Point-of-use inventory is consumable inventory that is used in the course of business operations, not sold as a retail item. For example, electrical contractors keep wire and electrical components on a job so they can make a EV charging station. Medical clinics keep consumable supplies like bandaids in clinics for use on patients. Amazon needs paper towels, soap, and other items referred to as Maintenance, Repair, and Operations (MRO) inventory in their fulfillment centers in order to keep the center running. Point-of-use inventory at a manufacturer means their “C” class parts, or parts of the lowest value, such as nuts, bolts and other fasteners. Plumbers and HVAC technicians have point-of-use inventory on their trucks like pipes and capacitors that they use in the course of finishing a service appointment.
What is Point-of-use Inventory Management?
Point-of-use inventory management requires a unique method of ordering, counting, tracking, and replenishing inventory that is located not on retail shelves or warehouses to be sold, but in stockrooms/trucks to be used. These locations are called the point-of-use. Depending on the business and the inventory type, the point-of-use might be a production floor, a service truck, a fulfillment center, a conex on a construction site, or an EMS vehicle. While point-of-sale solutions track retail inventory and Warehouse Management Systems track finished goods inventory to be sold, point-of-use inventory management solutions track and replenish inventory at the point-of-use. Special point-of-use software is required to track and auto-replenish inventory at these forward stocking locations in order to not run out of inventory or waste money by stocking too much.
"We onboarded just under 1000 items and are adding more daily. eTurns' customer service has gone above and beyond. TrackStock has decreased from 1 week to 1 day the time it takes us to do monthly physical inventory counts."
Key Differences Between Point-of-use and Traditional Inventory Systems
Most traditional inventory systems are designed to manage either, A) point-of-sale inventory - inventory that is directly for sale in a retail or e-commerce model, or B) manufacturing inventory such as raw materials, work-in-process, or finished goods. Point-of-sale software helps you track retail inventory sales. Material Resource Planning software ensures that you don’t stock out of the raw materials inventory that you need to build your product. On the other hand, Point-of-use inventory software does not address sales, manufacturing processes, or shipping details. Point-of-use inventory software is designed to track what inventory you use in the course of business, set minimum and maximum levels on each of those items, and automate the replenishment order management of those items.
Point-of-use vs. Warehouse Inventory Management Systems
A warehouse inventory management system is software that helps with the storage, tracking and movement of large boxes of inventory. Warehouse management software is concerned with the internal warehouse processes including storage, inventory retrieval, picking/packing/shipping, space and labor use. On the other hand, a point-of-use inventory system sits at the location where the material is used and is designed to track usage of individual pieces of consumable items that are used in the course of business, such as MRO items, medical consumables, or electrical parts. The “point” of the point-of-use management system is to not stockout at these locations while not wasting money on stocking too much inventory either.
Point-of-use vs. Retail Inventory Management
While both point-of-use inventory management and retail inventory management use QR codes and barcodes to scan inventory, each system works in a totally different environment. In retail, point-of-sale systems are used by an employee when they check out a customer and they are the main way that retail inventory is tracked. However that same store may need a point-of-use inventory app for the MRO inventory they use to run the store, such as janitorial supplies. Point-of-use inventory apps can be used for cycle counts, where a person scans the UPC code of the item, then types in how many items remain, then submits the count. Cycle count software like eTurns TrackStock compares each count to a minimum level set in the software, and triggers an order to a supplier if the item count is below the minimum threshold.
Point-of-use vs. E-commerce Inventory Management
A distributor often needs both an E-commerce inventory management solution as well as a point-of-use VMI or CMI inventory management software solution. They have different purposes. An e-commerce inventory management solution would require a distributor employee to take an order on an e-commerce site and then pick, pack and ship the item. Separately, in a point-of-use inventory management scenario, that distributor might give one of their technicians a (VMI) vendor-managed inventory app to go to their customer’s manufacturing floor and scan bins of items to do cycle counts that trigger replenishment of inventory that has fallen below a minimum.
The Benefits of Implementing Point-of-Use Inventory Management
Why is inventory management important, and how can point-of-use inventory management improve business outcomes? While point-of-use inventory management is not needed in every type of business, its benefits for certain organizations is notable.
Point-of-use Inventory Systems Can Track Lot Numbers, Serial Numbers and Expiration Dates
POU inventory systems allow for the tracking of lot numbers and expiration dates, which is of vital importance in the food and medical industries.
For lot numbers, TrackStock allows you to scan the item into inventory and get a list of the lot numbers that are still in inventory, which is especially helpful for cycle counts.
For expiration dates, TrackStock helps with the goal of limiting expired items. TrackStock can provide a scheduled report sent via email when items with expiration dates are within a range of days set for the Stockroom stating which items are nearing their expiration dates. When combined with TrackStock's AI Min/Max Tuning Dashboard analytics that optimize inventory levels, waste can be eliminated.
Point-of-use Inventory Systems Give Real-time Visibility
By managing inventory at the point-of-use, you can get much better visibility into item levels in that remote stocking location. Some POU inventory systems use inventory sensor technology like SensorBins weight sensors that sit under bins of product and give you real-time visiblity into stock levels and then automate replenishment.
Point-of-use Inventory Systems Help Avoid Stockouts
There is a real cost to stocking out of material that you need to run your business. If Amazon runs out of cardboard boxes they cannot conduct business. They don’t sell cardboard boxes, but they have to manage the inventory of cardboard boxes perfectly at the point-of-use. This is an example of a use case where point-of-use inventory management software is needed to manage MRO consumable material at the point-of-use in order to avoid stockouts.
Manage Consigned Inventory at the Point-of-use
When distributors stock and manage consigned inventory at a customer’s site, the distributor becomes a key inventory lifeline for the customer. Of course, consignment inventory only works if you have a point-of-use inventory management app to track usage of consignment inventory and consolidate billing. eTurns TrackStock makes consignment inventory management at the point-of-use easy.
How to Implement Point of Use Inventory Management
There are three main steps involved in setting up your point-of-use inventory management system:
- Decide on what Point-of-use Inventory Management Software you want to use. Look at this article for how to pick the best point-of-use mobile inventory app.
- Create a list of the items you want to replenish and upload the spreadsheet into the app. Details include: the product number, the package reorder quantity, the supplier name, location, minimum level and maximum level.
- Create QR codes or barcode labels for bins using an app like eTurns
Decisions to Make Before Implementing Point of Use Inventory Management
Decide on:
1. Ownership model: customer-owned inventory or consigned inventory
2. Replenishment method: Scan-to-order, Scan-to-cycle-count, Scan-to-consume material.
3. Which suppliers: Make sure your POU inventory app is supplier-independent.
4. What technology works best at the point-of-use based on space or labor constraints:
- Barcode scanning app for order management or cycle counts
- Electronic shelf labels
- RFID for digital kanban
- SensorBins for fully automated replenishment
5. How to customize your barcode labels: Customize QR or barcode labels with photos and data for scanning
6. What user-defined fields to use: Inventory management software like eTurns allows you to use user-defined fields for project-based cost-accounting and reporting.
"Global HOPE is using TrackStock to remotely track usage of the medical supplies and medicines we send to our facilities in Africa. TrackStock gives us the ability to deliver customized reports to our donors about how we are using their donations. It also helps us track lot numbers and expiration dates of the supplies. The app streamlines the entire replenishment process of tracking, ordering, reviewing, approving, purchasing, receiving, and reporting, all remotely from Texas!"