How to Cycle Count and Replenish Consumable Supplies
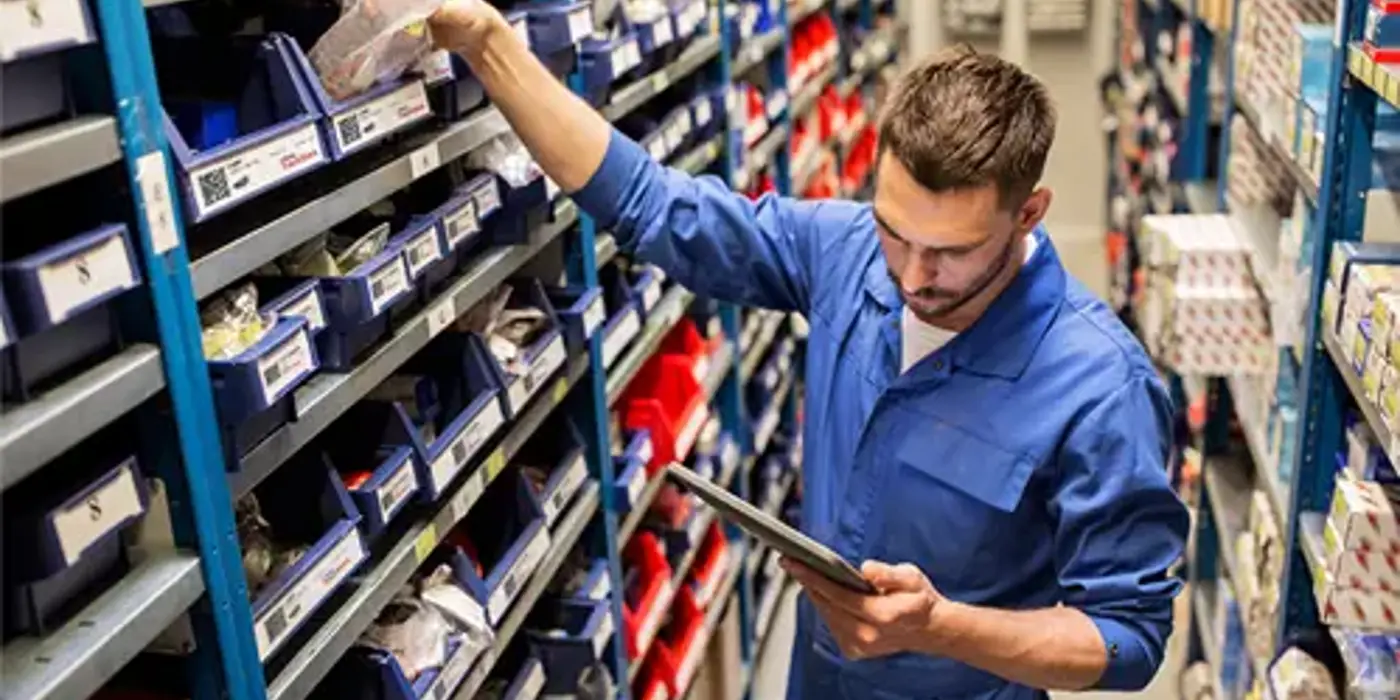
Introduction to Consumable Inventory Management
Consumable supplies are integral to the seamless operation of businesses, encompassing items that are regularly used up and need replenishing. Their short-lived nature demands a proactive approach to inventory management, ensuring that operations continue without interruption while avoiding costly and unnecessary overstock.
In this article, explore key inventory management and replenishment techniques for consumable supplies and discover how to strategically implement cycle counting. These principles can help organizations ensure operational continuity and build a leaner, more cost-effective business. By leveraging technology and adopting best practices in inventory management, companies can unlock new levels of efficiency, reduce waste, and stay competitive.
Understanding Consumable Supplies
In inventory management, most people think of product inventory – the inventory that a company sells or includes in the products they make. Alternatively, consumable inventory is used for ongoing business operations or for providing a service that customers pay for, and the management (or mismanagement) of it can have a big impact on profitability.
Because consumables supplies are used and replaced frequently, inventory management and replenishment of them can pose a challenge. It’s easy to underestimate the importance of efficiently managing consumable supplies, but these items are the backbone of daily operations for businesses across industries. Their management requires a nuanced approach to prevent both shortages, which can cause unexpected downtime, and excess, which ties up capital and storage space.
Examples of Consumable Supplies
Common examples of consumable inventory items include:
- Stationery supplies like printer paper
- Janitorial and sanitation supplies like trash bags
- Medical supplies like bandaids
- MRO industrial supplies like fasteners
- PPE like masks and gloves
- Breakroom supplies like drinks and chips
Consumable supplies can also be industry-specific items like napkins in food service, protective gloves in medical settings, and coolants in manufacturing.
Inventory Management Techniques for Consumables
Implementing a reliable inventory management system for consumables is crucial in the effort to protect uptime and preserve costs. Uncover the best way to track and replenish consumable supplies.
What Is The Best Way To Track and Replenish Consumable Supplies –VMI or CMI?
While just-in-time inventory management or ABC analysis for cycle counting can help answer “how” a company manages its inventory, just as important is the consideration of “who” will do that management. For that, companies should consider whether VMI (vendor managed inventory) or CMI (customer-managed inventory) will be the right method for optimizing the replenishment of their consumable supplies.
When companies do not have the administrative bandwidth to manage the consumable replenishment process yet they absolutely do not want to stock out of items, it’s common to use a Vendor Managed Inventory (VMI) approach to consumable inventory management.
In VMI, the supplier monitors stock levels once or twice a month, makes replenishment decisions, and has direct access to the company's consumable inventory data. This approach alleviates some of the workload for the organization, allows for frequent consumable inventory replenishment, and leverages supplier expertise about specific products.
On the other hand, VMI also has its drawbacks. This approach means that clients have to trust suppliers to control their inventory, which can, unfortunately, lead to overstocking or stockouts in between supplier visits. And VMI can come with a hefty upcharge for the supplier’s services as well.
An alternative approach to VMI inventory management is Customer Managed Inventory (CMI). In this strategy, the company must keep track of its own data and analytics to make informed decisions about minimum and maximum stock levels, reorder points, and inventory optimization.
"We onboarded just under 1000 items and are adding more daily. eTurns customer service has gone above and beyond. TrackStock has decreased from 1 week to 1 day the time it takes us to do monthly physical inventory counts."
Benefits of CMI for Consumable Supplies Management
With the proper tools and processes, embracing a CMI approach to consumable supplies management can yield impactful benefits. These benefits include:
- Cost savings on VMI Service Fees: Suppliers generally charge management fees under a VMI model. What’s more, organizations often struggle to ensure that the vendor is truly optimizing inventory levels and promoting the most cost-effective inventory management process possible. CMI allows for optimization and cost reduction when managed with the right automated replenishment software.
- Cost Savings on Item Upcharges: Most often, suppliers include a tremendous upcharge on all of the products they are managing using VMI. By “tremendous,” we mean 2 to 3X what the business can purchase the same products for with an automated replenishment solution using CMI to perform cycle counts.
- Increased Control: CMI gives the organization full control over its inventory, enabling them to fine-tune their inventory levels to meet their specific operational needs. The customer can do stock checks every day if desired instead of waiting for the supplier to visit one or two times a month.
- Data-driven Processes: When executed well, CMI relies on data analysis to optimize inventory, reducing waste and improving accuracy.
- Optimized Uptime: With firmer control over inventory and operations, businesses can reduce downtime by ensuring essential parts and supplies are always available.
The Role of Automated Replenishment in Optimizing Consumable Supplies
Automated replenishment systems have transformed how businesses manage consumable supplies. By using ongoing tracking and analytics of past use data, these systems can accurately optimize and predict the best time and quantity for the next order, triggering automated stock replenishment with minimal human intervention required. These automated stock replenishment systems reduce manual oversight, improve order accuracy, and ensure a steady supply of essential consumables, enhancing overall operational efficiency.
The Essentials of Cycle Counting
For many organizations, regardless of whether they use VMI or CMI inventory management, the best method for tracking and replenishing consumable supplies is through cycle counting.
What is Cycle Counting?
Instead of counting all inventory at once, the cycle counting method involves breaking your inventory down into categories and counting one category at a time. This systematic inventory auditing procedure takes place continuously without disrupting operations. Instead of shutting down shipping and receiving periodically for a full inventory count, organizations can use cycle counting to strategically count inventory little by little, without sacrificing productivity or accuracy.
Benefits of Implementing Cycle Counting for Consumable Supplies
Implementing cycle counting for consumable supplies offers numerous benefits, including increased inventory accuracy, reduced disruptions to operations, time savings, flexibility, and enhanced insight into inventory levels. With eTurns TrackStock, users can do cycle counts with an easy VMI/CMI inventory scanning app that applies min/max levels for each item and triggers automated stock replenishment orders as needed.
Best Practices for Implementing a Cycle Count and Replenishment System
Adopting a cycle count system for tracking and replenishing your consumable supplies doesn’t need to be complicated. With the right app and an accurate item list, you’ll have the new method up and running quickly.
Selecting the Right Cycle Count Software
It’s next to impossible to run a successful cycle count and replenishment system manually, so you’ll need to select inventory management software that best fits your business. Choosing the right inventory replenishment software is crucial for effective cycle counting and replenishment of consumables.
The ideal cycle count software should work offline and then sync (so WIFI doesn’t matter), set dynamic min/max levels for each item that trigger auto-replenishment orders to any supplier, be able to do ABC classification, show you any items you skipped in you count, and give you customizable reports that can be sent as email alerts. With cycle counting tools in eTurns TrackStock, organizations get all these capabilities.
In fact, eTurns recently became the CMI Replenishment App Provider for a large ecommerce provider with many fulfillment centers. They wanted to track and auto-replenish consumable supplies used by the employees to keep the center running. They had been getting overcharged by suppliers who were replenishing them in a vendor-managed inventory model, so they looked for a customer-managed inventory app and found everything they needed in eTurns.
How to Get Started With Cycle Counting
Integrating cycle counting into your inventory management routine requires a structured approach. You’ll need to categorize all inventory, upload your item list into your cycle count software, set a regular counting schedule, train staff on counting procedures, and set up your new software to send automated stock replenishment orders.
Key Takeaways on Cycle Counting and Replenishing Consumable Inventory
Overall, it’s important to understand the following about cycle counting and replenishing consumable inventory:
- Efficient management of consumable supplies is essential for seamless business operations and requires proactive inventory management techniques to avoid overstock and ensure continuous operation.
- Adopting cycle counting for consumable supplies increases inventory accuracy and reduces operational disruptions.
- Automated replenishment and cycle counting solutions like eTurns TrackStock offer precise tracking, reduce manual oversight, and ensure a steady supply of essential consumables, enhancing operational efficiency.
Future Trends in Inventory Management and Replenishment
Future trends in inventory management and replenishment are likely to focus on further automation with weight sensors like SensorBins and eLabels for inventory management, the integration of AI for predictive analytics, and more sustainable inventory practices. These advancements will continue to evolve the strategies businesses use to manage consumable supplies while driving efficiency and enhancing competitiveness.