Construction Inventory Management: 5 Tips for Successful Site Inventory Management
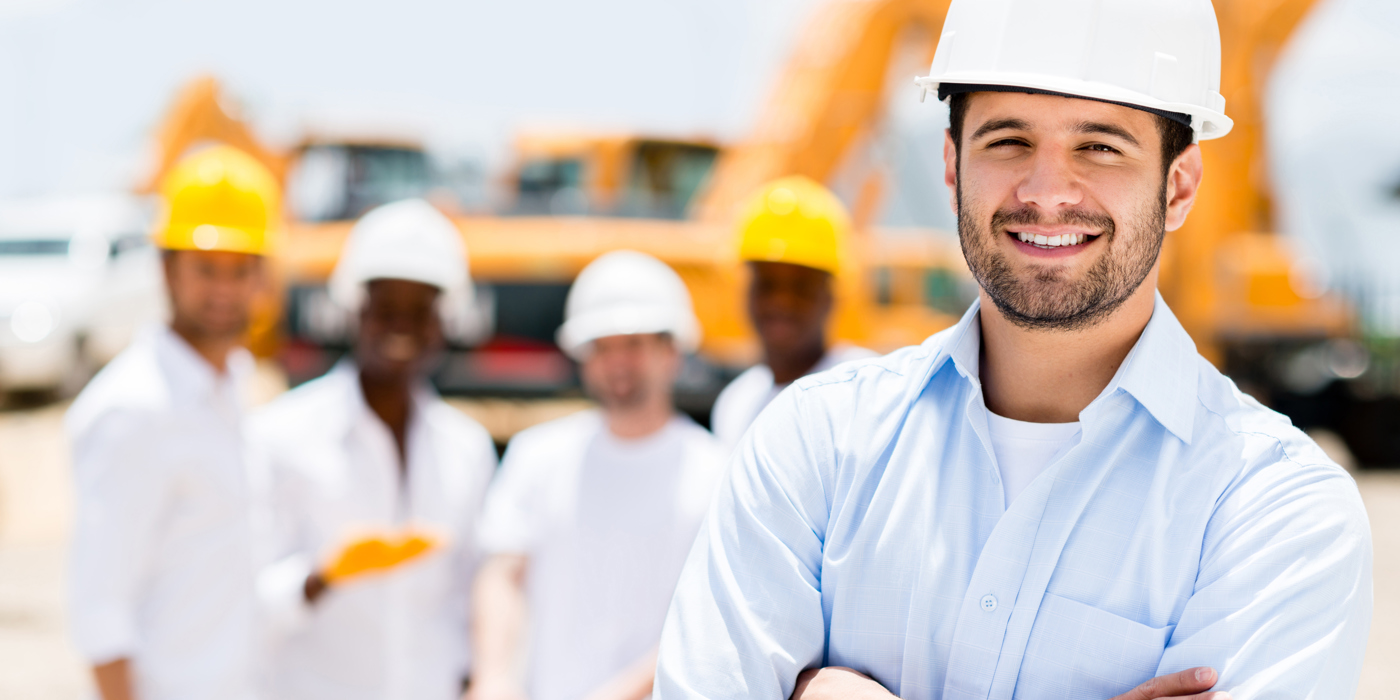
Anyone who has worked on a construction site knows these environments are full of many moving parts. With countless tools and supplies moving in and out of the site each day, it’s easy to lose track of inventory. Implementing an efficient and reliable construction inventory management system is crucial for the success of any construction project. The following five tips can help streamline processes, save costs, and improve efficiency overall.
1. Centralize Storage
The first step toward efficient construction material inventory management is knowing where each item is located. Centralizing storage allows for more reliable control over inventory because it facilitates reliable organization systems and more efficient tracking.
Using a dedicated storage container, or Conex, on each construction site immediately improves your team's overall productivity. Centralizing storage means less wasted time searching for the next tool and fewer items lost or misplaced.
Within the storage area, your team can formulate an organization system that each employee agrees to follow. This should include categorizing and labeling items for easy placement and tracking within the construction material inventory management strategy.
2. Secure All Inventory
Due to ongoing supply chain complications and challenges, price increases for various materials, and narrow profit margins on thousands of construction jobs, avoiding inventory loss is paramount. When shrinkage occurs, your teams must adapt to costly delays as they wait for the next shipment to be delivered, in addition to shouldering the negative financial impact of replacing lost supplies.
Misplaced items and inventory theft are best prevented by physical security solutions such as shipping containers (also called Conex containers), cages, or lock boxes. The exact combination of storage factors your employees use depends on the size and value of each item.
Here’s a table breaking down specific recommendations based on equipment categories:
Large Equipment |
Small Equipment |
|
Expensive Equipment |
Hard surface enclosure with lockbox or access control pad |
Custom-fitted hardshell carrying case with lock or equivalent solution |
Inexpensive Equipment |
Cage or large enclosure with key or digit combination padlock |
Simple, durable carrying case or portable tool rack |
If you don’t have the budget or space to implement all of the above storage solutions right away, don’t sweat it. Start with a simple, centralized storage location like a worksite van or storage container and develop it as you have the funds and time to do so.
Implementing access control best practices throughout your construction inventory management plan further secures your inventory. Instead of managing physical keys or passing around keycards, grant precise user access with construction inventory management software, like eTurns, that is designed specifically for contractors.
While all of your staff members need access to many of the materials, only managers need access to many of your tools at various times, only foreman and project leads need access to specific high-cost tools and equipment. Access management software boosts accountability by preventing unauthorized individuals from accessing your team's supplies and by tracking data about who accesses which equipment or materials, when, and how frequently.
One access management platform is BoxLock, which is used in conjunction with our TrackStock replenishment app to manage onsite inventory for a major US distributor at a large telecommunication company that constructs cell towers across the US. While we provide this distributor with the ability to track inventory usage, BoxLock provides access control and accountability without the expense of an inventory vending solution. It's a true end-to-end worksite solution.
3. Implement New Technology Solutions
Guessing games and resource-sucking processes that merely result in frustrating games of hide-and-seek ought to be a thing of the past. Instead, implement construction inventory management software as soon as feasible to track all materials and streamline your ordering processes.
Construction inventory management software such as eTurns TrackStock empowers project managers and foremen to:
- Access real-time data on stock levels
- Make informed decisions about procurement
- Avoid stock outs
- Minimize excess inventory, labor expenses, and carrying costs
- Streamline processes
With accurate visibility into your supply levels and easy ordering processes, construction inventory management software can vastly improve overall project efficiency.
4. Use Scanning Technology to Track Consumption
It's important to remember that human error isn't 100% avoidable. When construction project managers rely on pen-and-clipboard inventory management methods, mistakes are bound to occur. What’s more, even when perfectly executed, manual inventory tracking practices eat through valuable weekly labor hours.
Instead of relying on manual tracking, use scanning technology to track consumption. Barcode or RFID scanning systems allow your staff to quickly and accurately record material use. For example, your staff can use the TrackStock app to scan materials into the inventory system when they arrive at the construction site.
Then, as materials are used on site, technicians can easily scan them in the app and the on-hand inventory levels will be updated in real-time. This way, project managers always have accurate and up-to-date inventory data, without dedicating critical hours to manual inventory counts.
5. Tune Min/Maxes to Automate Replenishment
The final step in creating a streamlined and successful construction material inventory management system is determining the right quantity of materials to keep on-site. Keeping supply levels too low can result in stockouts and devastating delays. On the other hand, keeping a surplus of materials is likely to increase carrying costs and affect profitability.
Using the analytics provided by inventory management software can help project managers set min/max levels based on real usage. Min/max levels are the minimum and maximum quantities of any given item that should be kept in stock. Once min/max levels are set, construction inventory management software triggers automated alerts when an item reaches the minimum threshold. Then, an order is automatically created that will replenish the supply back up to the maximum level.
Min/max levels should be dynamic and tuned on an ongoing basis based on each project, actual usage, and lead times. TrackStock helps users keep optimized min/maxes settings with its Min/Max Tuning Dashboard.
With the right tools, it’s possible to transform inventory management processes from a pain point to a strength. By centralizing storage, securing inventory, implementing technology solutions, using scanning technology, and tuning min-max levels, your construction team can reduce costs and increase productivity. Contact us now to learn how eTurns introduces a whole new level of can efficiency to your construction projects.