Auto-Replenishment: The Secret to Lower Costs & More Efficiency
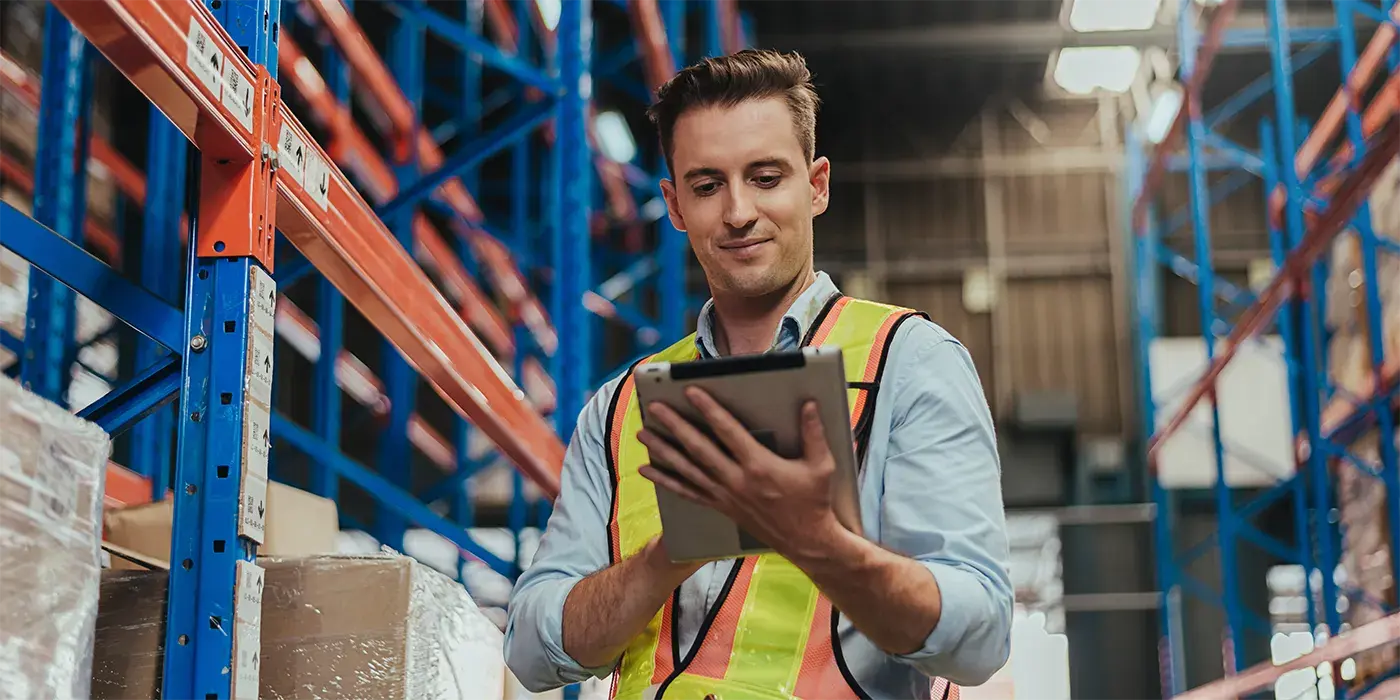
Automatic replenishment of point-of-use inventory is an inventory management system that maintains optimal inventory by using minimum and maximum (min/max) settings to trigger and automate the reordering process.
Instead of the time-consuming method of manually tracking stock levels and ordering with spreadsheets, your team can rely on an automatic system to replenish items as they reach predetermined minimum thresholds. These thresholds are often based on the average daily usage of each item, combined with lead times for restocking, creating a frictionless inventory management process.
Automatic replenishment is also more than just automated ordering—it uses data-driven insights to ensure inventory used in the course of business is replenished in the right quantities at the optimal reorder point. By considering actual consumption data and predictive min/max models, auto-replenishment optimizes inventory without manual intervention, giving your business invaluable peace of mind.
The importance of maintaining optimal stock levels can't be overstated in businesses and clinics with point-of-use inventory. Where running out of retail point-of-sale inventory may mean you lose a $10 sale, if you run out of certain types of point-of-use MRO or medical consumable inventory, you may have to shut down operations.
Auto-replenishment makes it easier to avoid the pitfalls of overstocking (which ties up capital) or stockouts (which disrupt your operations). Automatic replenishment is especially crucial if your business deals with high-volume inventory or relies on just-in-time (JIT) inventory management strategies.
What Types of Companies Need Auto-Replenishment?
One of the most significant advantages of auto-replenishment is its ability to transform remote inventory management where managing stock levels manually would otherwise be next to impossible. Companies that manage inventory in remote locations that they use in the course of business but don’t sell, whether that inventory is customer-owned inventory or consignment inventory, benefit the most from automatic systems of replenishment to avoid operational disruptions.
An auto-replenishment approach reduces operational complexity by ensuring stock is replaced as needed, allowing you to focus on core business functions like sales and marketing rather than inventory management. Auto-replenishment systems are used across dozens of industries, each with needs that are somewhat unique from the others.
Five industries that benefit from auto-replenishment for point-of-use inventory include:
-
Healthcare: Hospitals and clinics must maintain optimal levels of essential consumable medical supplies and medications to provide uninterrupted patient care. Automated ordering to keep items at par levels is helpful when staff have dozens of urgent tasks to fulfill every day.
-
Distribution: Distributors often manage large inventories for their customers in a VMI model across multiple locations. Auto-replenishment simplifies the replenishment of customer-owned inventory and consignment inventory, improving service levels and reducing operational complexity.
-
Maintenance, Repair, and Operations (MRO): Ensuring spare parts and critical maintenance supplies are always on hand is essential to prevent downtime and operational delays for MRO companies. Auto-replenishment systems streamline the management of parts inventories, ensuring that stock is automatically reordered when supplies reach pre-specified thresholds.
-
Emergency Medical Services (EMS): In emergency medical services, having the right supplies readily available is sometimes a matter of life or death. Auto-replenishment helps EMS providers maintain optimal stock levels of critical medical supplies on vehicles and in stockrooms, such as medications and first aid materials.
-
Service Trucks: Service trucks must be fully stocked with the right tools, parts, and materials to handle on-site jobs so that technicians don’t need to make extra stops to purchase parts. Auto-replenishment systems that include work orders that track inventory usage and automatically reorder supplies when stock runs low, ensure that each service truck is always prepared for the next job.
How Auto-Replenishment Works
Auto-replenishment, which is the process of automatically restocking products based on the ideal inventory amount and reorder point, works in tandem with inventory management platforms like eTurns TrackStock. As a distributor, TrackStock empowers you to lower your cost to serve and increase service levels by putting the replenishment process on autopilot. Here's how it works:
-
Min/Max Settings with Reorder Point Algorithms: TrackStock uses advanced algorithms to determine when items should be reordered. These algorithms take into account factors such as average daily usage and lead times. This means TrackStock calculates the optimal minimum and maximum stock settings for each item.
-
AI-Powered Dashboard: Users benefit from the AI Min/Max Dashboard that guides users how to adjust their minimum and maximum levels. You can gradually or immediately adjust these levels, ensuring your inventory stays in an optimized state while avoiding stockouts.
-
Cycle Counts & Consumption Pulls: The app facilitates efficient inventory replenishment through methods like cycle counting or consumption pulls. This supports accuracy and efficiency, as the system factors in real-time inventory usage when determining replenishment needs.
Our platform’s algorithms are particularly effective because they calculate reorder points by considering both your average daily usage of inventory items and the time it takes for your distributors to restock items for their customers. eTurns also factors in real-time data from cycle counts or consumption pulls and automatically adjusts the min/max levels for each item based on all available data.
This way, you ensure your business always has the right amount of inventory on hand without the need for manual intervention. As stock is used, TrackStock tracks consumption and places orders as necessary, freeing up your team’s time and maintaining accurate inventory levels.
5 Benefits of Auto-Replenishment
There are multiple auto-replenishment advantages experienced across business operations:
-
Reduced Manual Ordering: By automating the ordering process, your business significantly reduces the need for manual data entry and reordering tasks. This not only saves time but also reduces the risk of human error.
-
Increased Efficiency and Accuracy: Auto-replenishment systems like TrackStock improve the accuracy of stock levels by relying on point-of-use usage data and algorithms that constantly monitor inventory.
-
Stock Levels are Close to Optimal: With auto-replenishment, you’ll be confident that you always have the right amount of stock on hand, avoiding both overstocking (which drains profit) and stockouts (which pauses operations).
-
Improved Customer Satisfaction: By preventing stockouts, auto-replenishment makes sure your customers always have the inventory they need to conduct their business, boosting customer satisfaction and loyalty. This is especially important for industries where timely delivery is especially critical, including healthcare and manufacturing.
-
Stronger Supplier Relationships: Automatic replenishment fosters better communication between businesses and their distributors. With clear, data-driven reorder points, distributors can better anticipate demand and improve their own operations, driving confidence and stronger outcomes for their clients.
2 Challenges in Auto-Replenishment
Although auto-replenishment offers unmistakable benefits, there are two challenges to be aware of and plan for:
-
Supply Chain Variability: Auto-replenishment systems are vulnerable to supply chain disruptions. If your suppliers experience backorders or material shortages, the system can’t replenish stock in time, leading to potential delays. This is crucial to address in industries with unpredictable supply chains, like semiconductors and medical supplies. To mitigate this risk, maintain strong relationships with multiple suppliers and have supply chain disruption response methods ready to enact at any time.
-
Total Data Accuracy: The success of an auto-replenishment system hinges on the accuracy of the data input into the system. If your inventory data is incorrect due to poor cycle counting or human errors, the entire process can break down. This is why it’s critical to train your employees on TrackStock from day one, preserving your data integrity and reducing the likelihood that careless mistakes affect one or more entire workflows.
Distributors have long faced challenges in managing customer-owned and consignment inventory manually. However, thanks to solutions like TrackStock, these tasks are now manageable and scalable through automation.
5 Tips for Getting the Most Out of Auto-Replenishment
To fully capitalize on the benefits of auto-replenishment systems, your business should leverage these five advanced tips:
-
Utilize Scanners and Sensors: Integrating barcode scanners and sensors with your inventory management system allows for real-time updates on stock levels and consumption, providing near-perfect accuracy.
-
Implement VMI/CMI Order Capture Software: Vendor Managed Inventory (VMI) and Customer Managed Inventory (CMI) software allow your business to collaborate more effectively with suppliers or customers, ensuring seamless order fulfillment.
-
Track Inventory Usage Data: Monitoring consumption patterns with auto-replenishment software that adjusts min/max levels dynamically decreases costs, saves time, and frees up space. These specific min/max calculations and fine-tuned data tracking aren’t possible or as accurate with manual inventory tracking and replenishment solutions.
-
Regularly Audit and Review Inventory Data: Periodically review your inventory data to ensure accuracy and make necessary adjustments to the replenishment parameters. While auto-replenishment software can manage day-to-day stock levels, regular audits ensure that any data discrepancies are caught before they cause larger issues.
-
Customize Min/Max Levels for Different Items: Not all products need the same min/max levels. For high-turnover items, min/max levels may need to be more aggressive to prevent stockouts, while for slow-moving products, lower reorder points often work fine. Customize these settings for each of your product categories to maximize efficiency.
3 Recommendations for Implementing Auto-Replenishment in Your Business
Implementing an auto-replenishment system and achieving desired results in the shortest period of time requires thoughtful planning and meticulous execution. Here are three ways to make the process as smooth as possible:
-
Start small. Begin by applying auto-replenishment to a select number of products or a single category. This makes it easier for your business to test the system, identify any issues, and make needed adjustments before expanding to all your point-of-use inventory.
-
Prioritize data capture with the right auto-replenishment app. Invest in robust data collection and management tools to ensure your auto-replenishment system has access to reliable information. Periodically review and clean your data to prevent errors that may cause inventory mismanagement.
-
Collaborate closely with your suppliers. This is arguably the most important step for the success of your auto-replenishment program. Establish dependable communication channels before any changes occur and double check that your suppliers are aligned with your replenishment strategies. Sharing goals and methods from day one prevents costly realignment or the potential loss of a partnership later on.
What Does the Future of Auto-Replenishment Look Like?
Auto-replenishment solutions will become even more sophisticated as AI and predictive analytics play a larger role in the near-term future. Instead of relying solely on historical data and average daily usage rates, future software and solutions will predict demand fluctuations based on broader market conditions, customer behavior trends, and seasonal factors.
We can also expect the rise of fully automated supply chains in the near future. From smart warehouses using robots to physically manage inventory to AI agents autonomously negotiating orders with suppliers, auto-replenishment will play a critical role in this emerging landscape. With the integration of Internet of Things (IoT) technology, every item could be tracked in real-time. This will foster unprecedented accuracy and efficiency in inventory management for most, if not all industries.
eTurns plans to integrate such AI agent technology into our software as well. This functionality can generate actionable “to-do lists” for users based on inventory usage data that we currently track for users, and can integrate with AI agents in the future. AI agents hold the power to further automate decision-making and reduce the need for human intervention.
eTurns TrackStock is flexible, scalable, and cost-efficient, making our platform suitable for both small businesses and enterprise-level operations. Start your free 30-day trial now to see the difference it makes firsthand.