6 Effective Inventory Reduction Strategies for Stockrooms
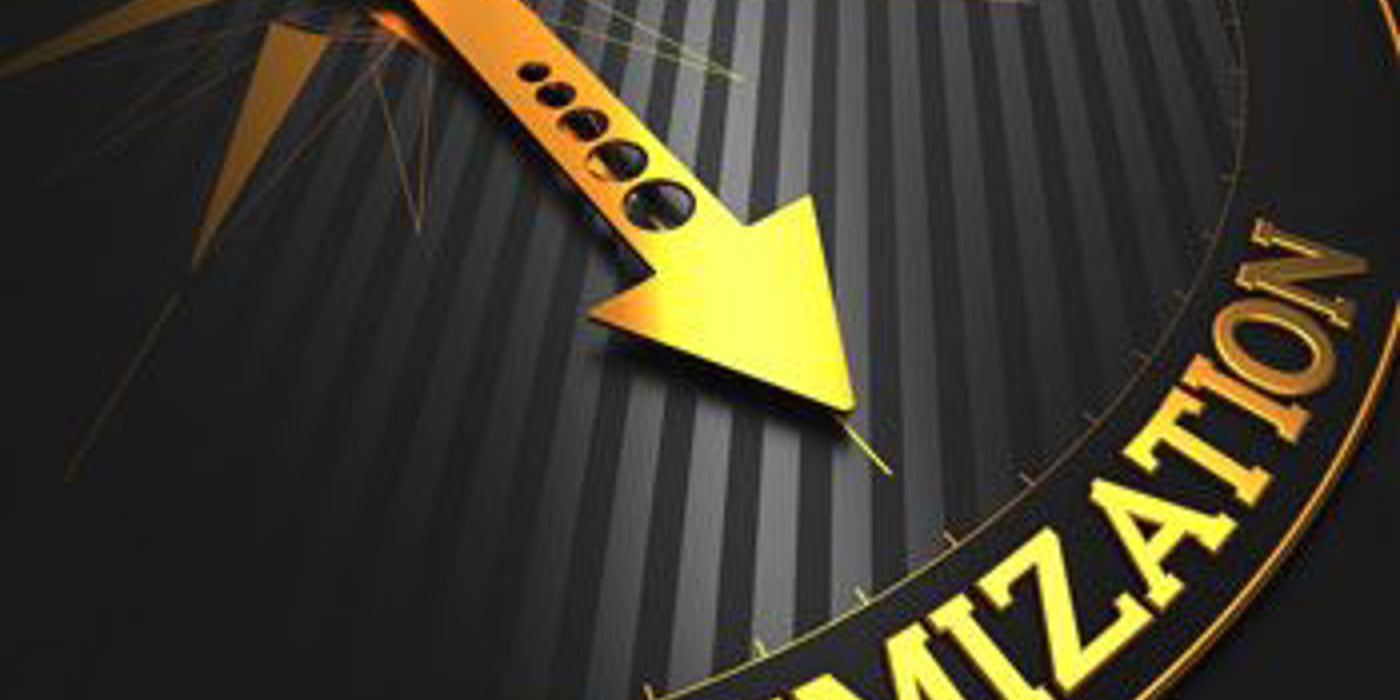
Stockroom and service truck inventory managers have typically stocked inventory so there’s always product to meet demand, even if it means overstocking product. We hear this across the board from managers of manufacturer MRO stockrooms, contractor jobsites and trucks, as well as medical clinics. But the days where inefficient use of cash was tolerated are over, and we have few helpful inventory reduction tactics you can use to kick off an efficient 2022.
The past few years have been tough for inventory managers, but going forward, they should double down on employing lean inventory strategies that will enable them to survive in today’s competitive market. With more competitors and rapidly changing products, stocking too much of a product can leave inventory managers holding on to expensive or obsolete items. Their primary objective should now be to digitize and optimize replenishment because that is the best way to carry enough inventory to meet demand while reducing the total amount of inventory in stock. And that is difficult to do without an inventory replenishment app.
eTurns TrackStock, an inventory replenishment app for point-of-use inventory, allows inventory managers to optimize and reduce inventory levels in stockrooms, trucks and connexes, and therefore lower costs and free up capital for other areas of the business.
Why is inventory reduction important? Carrying costs.
It’s not free to store inventory; the business expenses related to holding and storing unsold or unused goods are carrying costs. This includes the cost of the facility itself, utilities and employee salaries. It can also include transportation and handling, taxes and insurance, as well as depreciation, perishability or shrinkage from theft, damage or human error.
Carrying costs can add up to a big percentage of a company’s total inventory value and can range from 25% to 55%. Yes – up to 55%! Taking a few steps to reduce some of these costs can reap significant savings.
What are the benefits of reducing inventory?
Aside from the cost of the inventory itself, there are many benefits from reducing inventory levels, which include:
- Reduced storage costs - Reducing the amount of inventory in a stockroom, service truck or other stocking site, can reduce floor space and fees such as rental, storage, maintenance and labor to move inventory.
- Reduced obsolete stock - By optimizing the inventory in point-of-use locations, inventory managers turn over product more quickly, thereby reducing the chances of a part becoming obsolete or dead inventory.
- Freed working capital - Reducing inventory means the organization has cash to invest in other parts of the business. This also allows inventory managers to divert resources in one direction instead of another so they don’t lose opportunities for growth.
- Adaptability to market changes: Because they have less tied up in unused inventory, inventory managers have more flexibility to adjust to rapid market changes. Knowing what quantity of parts are used in real-time gives the inventory manager accurate data to make informed decisions on what parts to buy and how much to stock.
6 Inventory reduction tactics
The team at eTurns has been in the business of point-of-use inventory replenishment and VMI/CMI for over 20 years and have a few effective tactics to reduce your inventory levels:
1) Automate or digitize inventory replenishment as much as possible.
Everyone knows that ordering with a pencil and clipboard leads to overstocking and stockouts. Even using an e-commerce site can require rekeying product numbers and other steps than can take up to 10x longer than a simple-to-use replenishment app that digitizes your reordering. eTurns TrackStock uses phone scans, RFID, or IoT weight sensors to track usage and automate replenishment, depending on the organization’s needs. TrackStock RFID automates Kanban 2-bin replenishment and TrackStock SensorBins™ provide fully automated no-touch cycle counting and replenishment.
2) Consolidate your view of all your inventory.
Use one app to replenish from all suppliers. Using a multi-supplier inventory replenishment app gives you one view of all your inventory and orders so you don’t order too much. Get analytics and reports that show you where inventory resides across all your locations and implements transfers when needed.
3) Use an app that tracks usage and automatically triggers reordering.
Don’t order more if you aren’t using it. Traditional demand planning software simply aggregates past orders and makes assumptions about future demand, an error-prone process. With eTurns TrackStock apps, inventory managers use phone scans and sensors to track usage and trigger automated orders that allow them to optimize their stockrooms or service trucks.
4) Set Min/Max levels with guidance from usage analytics.
Setting min/max levels are a best practice for lean inventory management. And when a minimum has been met, you want to make sure that your system sends you an alert that is easy to act on to approve an order with one tap. After 45 days of using eTurns TrackStock for reordering, TrackStock’s Min/Max Tuning Dashboard is able to calculate what your min/max levels should be in order to enjoy optimized inventory levels and prevent stockouts or unnecessary orders. eTurns also sends email alerts to managers with one touch reordering from within the email to keep your replenishment moving forward efficiently.
5) Reduce obsolete and slow-moving inventory.
When you digitize your replenishment, you can keep tabs on expiration dates and lot numbers to make sure you use the oldest product first, if it is a medical product, and don’t waste money stocking obsolete inventory. User-defined fields in eTurns help users categorize lifecycles for products to easily identify slow-moving or dead inventory.
6) Get a dashboard that tells you exactly how much cash you can save through reducing inventory to calculated Min/Max levels.
eTurns TrackStock’s Min/Max Tuning Dashboard tells you how much money you can save by adjusting your inventory to the optimized min/max levels calculated after 45 days of tracking usage.
Start eTurns Free or Schedule a 30 Minute Meeting With Us to Learn More