2 Inventory Trends to Watch in 2025: AI & Sensor Technology
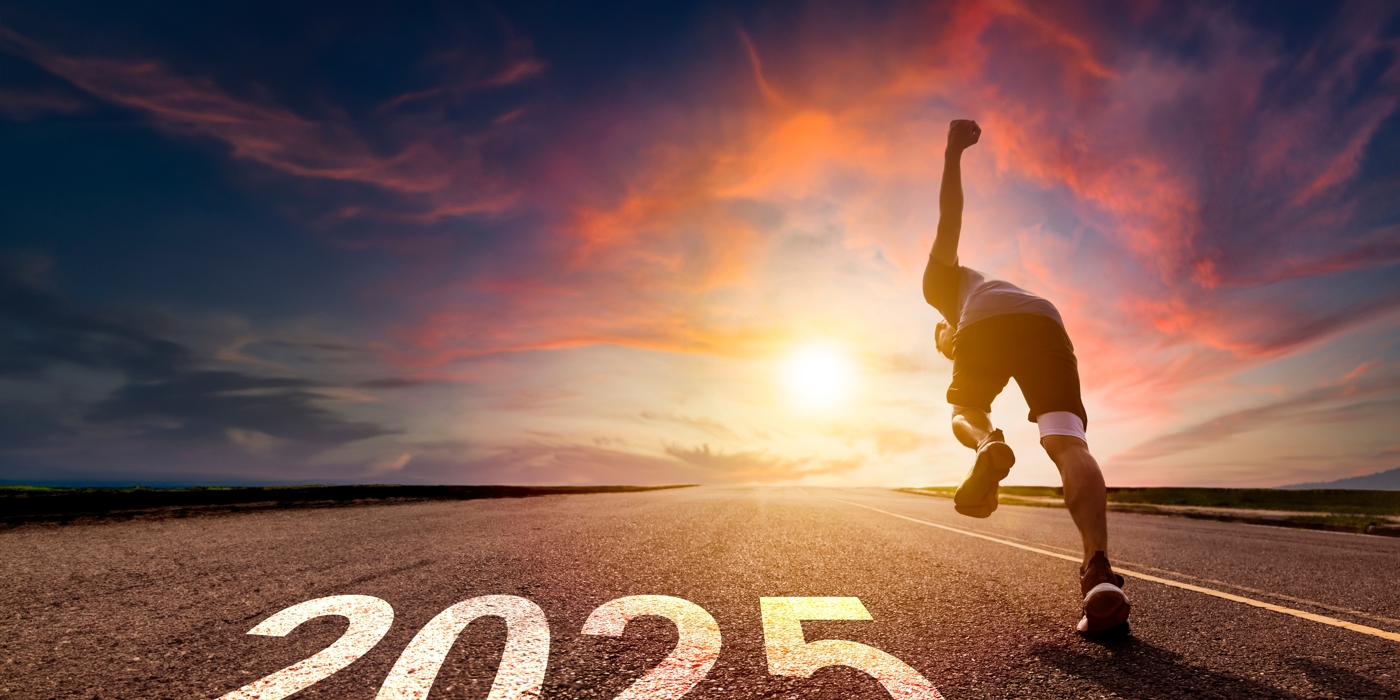
Inventory management at the point-of-use is no longer merely a nice-to-have—it’s the last 10 feet of the supply chain and the first 10 feet of the demand chain and it’s critical. It’s the only place to track what products are being used in the course of business, how their being used, for what projects, and how to optimize replenishment. Optimized inventory management of consumables at the point-of-use is a key opportunity for improving your profitability, efficiency, and customer satisfaction.
Traditional inventory methods—manual cycle counts, spreadsheets, and reactive ordering—have become inadequate in today’s data-driven world. They leave businesses vulnerable to errors, inefficiencies, and wasted resources. To stay competitive, distributors and the companies they serve are turning to leading solutions like artificial intelligence (AI) and inventory sensors to gain near real-time visibility, streamline replenishment, and make smarter, proactive decisions.
In this article, we’ll explore the top two inventory management trends to watch in 2025, including how AI and sensor technology are revolutionizing consumable inventory tracking, auto-replenishment, and optimization. Let’s dive in.
Artificial Intelligence (AI) in Inventory Management
Artificial Intelligence (AI) has transformed inventory management from a reactive process into a data-driven, predictive powerhouse. In the midst of these significant changes, it’s important to remember AI isn’t one-size-fits-all.
It includes multiple types of AI, each serving distinct purposes. Let’s look at the three types you need to know:
-
Predictive AI: This AI analyzes historical data and patterns to forecast future demand, optimize inventory levels, and reduce stock outs or overstock situations. Most AI-driven demand forecasting systems use predictive AI to determine what stock will be needed and when.
-
Generative AI: Unlike predictive AI, generative AI can create new data outputs based on learned patterns. In inventory management, it can generate reports, automated insights, and even customer demand scenarios to help managers prepare for unexpected market shifts.
-
Agentic AI: This is the most autonomous form of AI, capable of making real-time decisions without human intervention. In inventory automation, agentic AI can dynamically adjust reorder points, select alternate suppliers, and reallocate stock based on real-time changes in demand.
By leveraging the right type/s of AI, your business can automate replenishment, optimize stock levels, and gain deep insights into demand patterns—eliminating guesswork and costly errors. Here are the three ways AI is shaping inventory management in 2025:
1. Automated Inventory Replenishment with Predictive AI
AI eliminates the time-consuming task of calculating optimized min/max levels for replenishment. By integrating with inventory consumption data, AI can:
-
Trigger automatic purchase orders when stock reaches a predefined threshold.
-
Adjust min/max levels dynamically based on usage trends.
-
Reduce procurement costs by automating replenishment with integrated ordering.
Our AI Min/Max Dashboard continuously refines replenishment parameters, ensuring your business maintains the right inventory levels without over-ordering.
2. AI-Powered Inventory Insights with Predictive AI
AI doesn’t just track numbers—it provides actionable insights. When your business is using AI, you can:
-
Identify slow-moving stock.
-
Dynamically adjust minimum and maximum thresholds to keep optimum levels of inventory
-
Forecast what products customers will order in what quantity on what date.
Our AI Min/Max Dashboard is designed to:
-
Display the amount you can save in inventory and carrying costs by reducing inventory to the optimized levels TrackStock recommends
-
Improve replenishment efficiency through automated triggers.
-
Provide analytics for better decision-making.
As AI continues to evolve, companies that adopt smart inventory systems will gain a necessary competitive edge—reducing costs, increasing efficiency, and improving client retention.
3. AI Copilots: Your Smart Inventory Assistant
AI copilots act as digital assistants for inventory managers, providing real-time recommendations, automated alerts, and intelligent reorder suggestions. Instead of manually setting min/max levels, an AI copilot analyzes historical data, point-of-use usage data, seasonality trends, and order cycles to optimize replenishment.
Example Use Case: A distributor using an AI copilot receives automated recommendations like:
- "How many of my items are being stocked above optimized levels based on usage over the past 6 months.”
- "Stock levels for Item X are consistently running low. Increase the minimum setting by 15%."
- "Demand for Product Y has dropped by 30% over the past quarter. Reduce minimum and maximum settings by 30% to avoid overstocking."
- "Based on supplier lead times, reorder Item Z now to avoid a projected stockout next month."
When tapping into AI copilots, you’ll eliminate guesswork, reduce ordering mistakes, and optimize stock levels effortlessly.
Beyond Forecasting: AI’s Expanding Role in Inventory Optimization
AI continues transforming inventory management beyond demand forecasting and replenishment. Here are four more AI applications that improve supply chain efficiency and accuracy:
-
Fraud Detection and Anomaly Identification: AI now analyzes inventory movement patterns to detect discrepancies in stock levels, reducing theft and fraud. If an unusual number of high-value items are being reported as damaged or lost, AI flags the issue for review.
-
Automated Auditing & Cycle Counting: AI-powered inventory system can automatically track cycle counts with cameras, drones and robots. AI also identifies errors in inventory reconciliation, ensuring greater accuracy.
-
Supplier Risk Assessment: AI evaluates supplier reliability based on past delivery times, quality issues, and pricing fluctuations. If a supplier frequently delivers late, your AI will recommend alternative vendors to maintain smooth operations.
-
Inventory Cost Reduction Strategies: AI assesses carrying costs, procurement expenses, and warehousing inefficiencies to recommend areas for cost savings. It recommends better purchasing windows, dynamic safety stock levels, and storage optimizations–all in a fraction of the time that humans would do the same.
AI-Powered Search for Instant Inventory Data
Traditional inventory searches mean users are manually sifting through databases or spreadsheets to find stock levels, supplier data, and order histories. Generative AI revolutionizes this process by enabling natural language search queries, dramatically improving efficiency.
Instead of manually searching a database for "Current stock levels of medical supplies at Location A," AI-powered search tools can empower your team to ask in plain language, queries such as:
-
"How much PPE inventory do we have left in the Chicago facility?"
-
"What were my highest-demand items over the last three months."
-
"What products are consistently overstocked in our warehouse?"
These types of queries accelerate decision-making and improve accuracy. Instead of wading through endless screens of technical info, your search starts with the outcome you need.
8 Benefits and 3 Use Cases of Sensor Technology in Inventory Management
As your team strives for greater efficiency and accuracy with point-of-use inventory management, sensor technology should be a top priority for auto-replenishment and inventory usage tracking. By utilizing electronic shelf labels, RFID, and smart shelves for weight-based tracking your business will gain inventory visibility, reduce errors and reduce costs.
1. SensorBins for Automated Inventory Replenishment
One of the most impactful applications of sensor technology in inventory management is SensorBins—smart bins equipped with weight sensors that monitor stock levels in real time. These bins automatically trigger replenishment orders when inventory reaches a predefined threshold, eliminating the need for manual counting.
4 Key Benefits of SensorBins:
-
Real-time inventory monitoring: Prevents stockouts and overstocking.
-
Automated reordering: Reduces human error and labor costs.
-
Faster replenishment cycles: Ensures essential supplies are always available.
-
Data-driven optimization: Tracks consumption trends to refine inventory policies.
Industry Use Cases:
Manufacturing
-
Use case #1: Remote monitoring and auto-replenishing:
In the manufacturing sector, companies have implemented eTurns SensorBins in remote manufacturing sites where distributors need to know when to resupply their product. Etched is a company that makes metal name plates and they use SensorBins at their customer location, a motor manufacturing plant, to automate the replenishment of the different sized name plates as they are taken out of a bin. Distributors can use SensorBins as a productivity multiplier for a VMI sales rep that doesn’t have to visit remote sites as often.
-
Use case #2: Carts with weight sensors for counting and auto-replenishing:
A food service machinery company uses SensorBins on a cart with a cloud converter and mobile Wi-Fi (Mi-Fi) to help their techs count the items needed to build equipment. The techs roll the cart around the floor and use the SensorBins as an inexpensive counting scale to count what they need to fill a bill of materials to go build something. SensorBins reduce the time it takes to count, increase the accuracy of the count, and when supply hits a minimum, it sends an auto-replenishment order to the supplier.
-
Use case #3: Wireless mobile rack to resupply workstations and auto-replenish the rack:
These were created for electrical distributors to offer their electrical contractors customers. Contractors can keep electrical parts in battery operated SensorBins on the rack. The contractor can move the rack around the construction site and have all the electrical equipment conveniently on hand to use. When supplies on the rack hit a minimum, the SensorBins trigger an automated order to the supplier for replenishment.
2. Electronic Shelf Labels (eLabels) for Smart Replenishment at the Push of a Button
Electronic Shelf Labels (eLabels) trigger replenishment with the push of a button. These digital labels are linked to an inventory management system. When the user has visually confirmed that the reorder point has been reached, he pushes the button to send a digital order to the supplier. eLabels display important information such as minimum/maximum levels, or par levels (reorder points), and whether the item is on order, back ordered, or shipped as it moves through the supply chain.
4 Advantages of eLabels:
-
Accurate replenishment for consumable inventory in stockrooms, clinics, vehicles
-
Seamless integration with automated ordering systems.
-
Improved customer experience when medical practitioners have to spend less time on inventory replenishment orders
-
Labor efficiency, reducing the need for manual counting and ordering.
Industry Use Case:
-
Healthcare and Medical Supply Management Use Case:
Hospitals and clinics can use eLabels to keep track of critical consumable medical supplies. For example, one of the largest phone manufacturers in the US uses TrackStock eLabels in their in-house medical clinics in Silicon Valley to trigger replenishment with the push of a button and to save their practitioners time replenishing inventory.
3. Integration with eTurns TrackStock for a Complete Solution
eTurns TrackStock seamlessly integrates with SensorBins and eLabels to create fully automated inventory replenishment systems. Our clients using TrackStock benefit from:
-
Automated real-time tracking of inventory levels.
-
Hands-free replenishment for reduced procurement costs.
-
Improved inventory accuracy and visibility.
-
Decreased labor costs by eliminating manual cycle counts.
As businesses adopt sensor-driven inventory management, they gain an edge in efficiency and cost savings.The combination of real-time monitoring and auto-replenishment with less human labor ensures that businesses can operate with minimal waste and maximum profitability.
The Inventory Manager's Guide to 2025: Adapting to AI and Sensor Technologies
Adopting AI inventory management technology and innovative sensor-based tools into your inventory management processes is exciting, but it may also feel overwhelming. However, the process of adapting to the use of these tools on your team is well worth it in the long run.
Best Practices for Inventory Managers in the AI Era
As AI and automation continue to transform inventory management, it’s crucial for inventory managers to adapt and embrace these technological advancements. Below are best practices that empower you or your inventory managers to leverage AI tools effectively and maximize efficiency in inventory processes.
1. Invest in AI Training and Upskilling
AI-powered systems can be incredibly beneficial, but they require a knowledgeable workforce to use them effectively. Inventory managers should prioritize ongoing training and upskilling to understand how AI systems work and how to interpret AI-driven insights.
Best Practice:
-
Conduct Regular Training: Schedule monthly or quarterly workshops where teams are introduced to AI-powered tools and how to use them for demand forecasting, inventory replenishment, and supply chain optimization. This keeps the team updated with the latest features and best practices.
-
Example: Nike invests heavily in AI-driven tools to track inventory and sales trends. They continuously train their staff to understand AI-generated recommendations, ensuring the company maintains a lean and efficient inventory system. (Source: Business Insider)
2. Foster a Data-Driven Culture
Inventory managers should build a culture that embraces data-driven decision-making. AI relies heavily on data, and the more high-quality data available, the better the outcomes. Managers should emphasize the importance of accurate data entry and encourage the team to consistently gather and use data for decision-making.
Best Practice:
-
Promote Data Quality: Ensure that inventory data is accurate, up-to-date, and complete. Implement automated tools for continuous data monitoring to detect discrepancies and resolve them quickly.
-
Example: Unilever uses advanced data analytics and AI for inventory forecasting. By focusing on clean and high-quality data, Unilever improves decision-making, reducing excess stock and improving its supply chain strategy. (Deloitte)
3. Embrace AI for Real-Time Inventory Visibility
AI can provide real-time insights into inventory, helping inventory managers avoid costly stockouts or overstocking. Managers should incorporate AI-based systems that offer continuous updates on stock levels and help prioritize reorders based on predictive demand patterns.
Best Practice:
-
Adopt Real-Time AI Tools: Integrate AI-driven inventory management software, like eTurns, that offers predictive analysis and real-time updates for inventory replenishment. This ensures you’re always on top of stock levels and can act quickly when supplies are running low.
-
Example: L’Oréal uses AI to automate replenishment processes by tracking stock levels across various sales channels in real-time. This minimizes stockouts and allows the company to respond immediately to customer demands, ensuring optimal product availability. (Forbes)
4. Implement Continuous Improvement Strategies
AI systems are constantly evolving, so inventory managers must continuously optimize processes. Conduct regular assessments of AI-driven systems and adjust strategies based on performance metrics such as stockouts, order fulfillment speed, and inventory turnover.
Best Practice:
-
Monitor Performance Regularly: Set KPIs for inventory turnover, lead time, and stock replenishment accuracy. Use AI to measure the performance of these metrics and refine strategies accordingly.
-
Example: Target leverages its advanced AI-powered analytics to continually monitor stock levels across its network of stores and warehouses. This allows Target to adjust replenishment schedules to meet customer demand, optimizing supply chain efficiency. (Wired)
5. Collaborate with IT and Data Science Teams
As AI solutions evolve, inventory managers must work closely with IT and data science teams to ensure seamless integration of AI systems into their operations. This collaboration ensures that AI tools are effectively tailored to meet specific business needs and inventory requirements.
Best Practice:
-
Establish Cross-Department Collaboration: Set up regular meetings with IT and data teams to discuss data requirements, integration challenges, and optimization opportunities for AI systems.
-
Example: Coca-Cola uses collaborative teams to continuously improve its AI-driven demand forecasting system. By collaborating with data scientists and IT, Coca-Cola has been able to better predict demand surges and stock shortages, ensuring product availability while reducing excess inventory. (Supply Chain 24/7)
6. Start Small and Scale Gradually
When implementing AI-powered inventory systems, it’s a good idea to start small and scale gradually. Inventory managers should focus on implementing AI solutions in high-priority areas, such as demand forecasting or stock replenishment, and expand their usage over time as they gain confidence in the system’s effectiveness.
Best Practice:
-
Pilot AI Systems in Key Areas: Begin by introducing AI tools in specific segments of the inventory process and evaluate their performance before expanding usage to other areas.
-
Example: Carrefour, a global supermarket chain, began by testing AI in a few selected locations to optimize inventory for fast-moving consumer goods. Once the system showed positive results, it was rolled out to its larger operations. (Business Insider)
7. Keep a Focus on Human Oversight
While AI provides immense benefits, it’s crucial to retain human oversight in decision-making processes, especially for complex or unexpected situations. Inventory managers should balance AI recommendations with human judgment, ensuring that AI complements, rather than replaces, traditional management expertise.
Best Practice:
-
Establish a Review System: Use AI to automate basic tasks, but ensure that inventory managers regularly review AI-driven forecasts and actions to confirm that they align with company goals.
-
Example: Walmart utilizes AI to predict inventory levels across its network of stores. However, the company’s managers still review the AI recommendations and adjust stock levels based on regional preferences and seasonal trends, combining AI with human expertise for optimal inventory decisions (TechCrunch).
Implementing and Benefiting from Advanced Inventory Systems
To fully reap the benefits of AI and sensor technologies, businesses must invest in advanced inventory systems that truly fit their needs. Not all AI and sensor technology solutions are created equal, and some are a better fit for use cases with very specific parameters. Delving into the features of each tool available can help you select the best advanced inventory systems for your needs.
Make 2025 the year you investigate if AI inventory management or weight sensor replenishment can remove the friction from inventory replenishment in your business.
eTurns TrackStock is a leader in both of these inventory management systems. With a wide range of advanced tools for improved data analysis, automated tracking, and easy replenishment, we equip businesses and clinics to save time and money on replenishing consumable supplies.
To find out if we’re the best fit for your unique needs, get a free trial!